Pattern Making (Wax Injection) & Pattern Assembly
Pattern making is a foundational step in the investment casting process. Our skilled craftsmen, combined with advanced technology, ensure the creation of precise, high-quality wax patterns that serve as blueprints for our customers’ components. By meticulously designing and fabricating these patterns, we guarantee accurate dimensions and superior finish, setting the stage for reliable and efficient production.
Wax injection is performed using modern semi-automatic wax injection presses. Wax conditioning tanks are utilized for homogeneous wax mixing and temperature control. Assembly is conducted with environmentally friendly and safe miniature torches. Wax is recycled through a well-equipped wax recycling plant.
-
Centralized Air-Conditioned Area
-
Vertical Injection Press Machines: 02 Nos, 35 Ton Capacity
-
Horizontal Injection Press Machines: 04 Nos, 30 Ton Capacity
-
Separate Pattern Assembly Area
Shelling
Critical primary sand coating is carried out using a modern Rainfall Sander. The best available ceramic sand is used for both primary and secondary shelling without compromising on quality. For proper curing, temperature and humidity are controlled, along with forced air circulation in the shell drying rooms.
-
Centralized Air-Conditioned Area
-
Primary/Secondary Coating: Dedicated separate rooms
-
Back-up Coating Area: Separate room
-
Controlled Atmosphere: Temperature, Humidity, Air flow & Dust Control.
-
Separate centralised AC unit and Dehumidifiers for each room
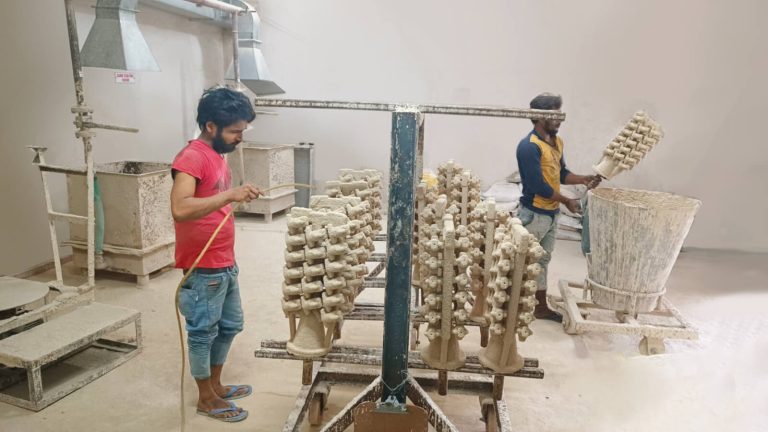
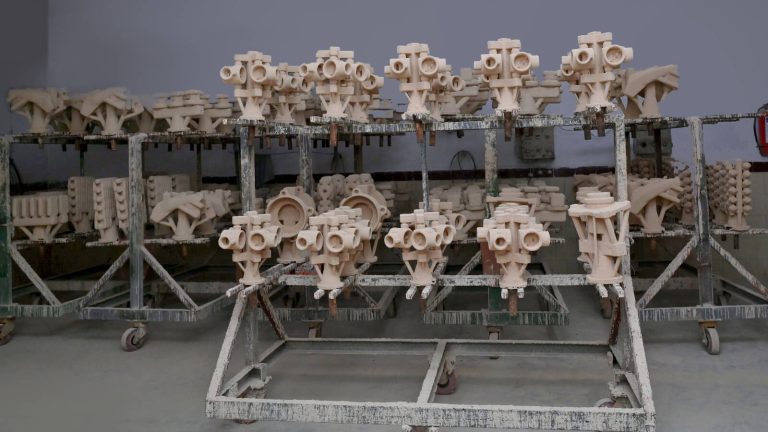
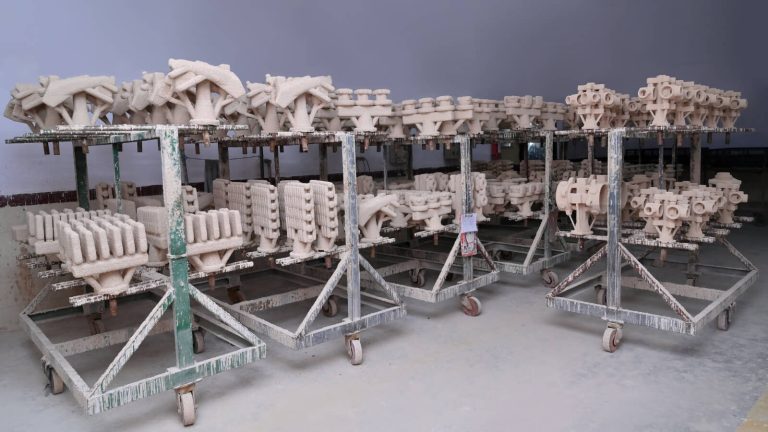
Melting
Ceramic shells are preheated in an environmentally friendly, modern shell-firing furnace to ensure uniform and optimal sintering of the shells. At GIPL, the melting and casting processes involve advanced techniques to heat metal alloys to precise temperatures before casting them into intricate molds, creating components with exact specifications.
-
250 KW Indopower furnace with 300 kg and 150 kg crucibles
-
175 KW Inductotherm furnace with 250 kg, 150 kg, and 50 kg crucibles
Heat Treatment
Castings are heat-treated using a well-equipped heat treatment furnace and a state-of-the-art quenching facility. The heat treatment process is monitored and recorded with an electronic data logger. Our experienced metallurgists provide solutions to meet material strength, machining, and forming requirements by adjusting the heat treatment cycles.
-
Muffle Furnace – 1200°C for sampling/qualification
-
Electric Coil Pit-Type Furnace for mass production – 1-ton capacity
-
Data Logger for cycle recording
-
Jib Crane for loading/unloading to furnace
-
Water Tank for quenching
-
Oil Tank for quenching
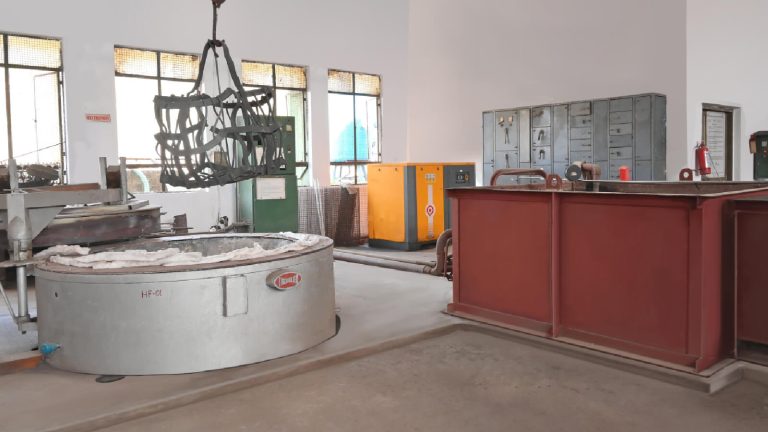
Fettling
Fettling and finishing at GIPL involve the process of cleaning and refining cast metal components to achieve precise specifications and a high-quality surface finish. This ensures that the final products meet stringent standards for both aesthetics and functionality, contributing to their overall performance and durability in various applications.
-
Hand Grinders
-
Swing Grinders
-
Abrasive Cutting Wheels
-
Painting Area
-
Abrasive Blasting
-
Arc covvect and TIG Welding Machines
-
Pneumatic Knockout Machines
-
Pickling and Passivation Facility
-
Coining Press